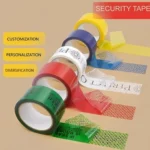
What Material is Tamper Evident Tape Made Of?
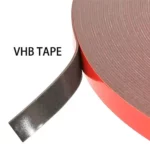
VHB Foam Tape
Industrial tapes are widely used in electronics, automotive, construction, and packaging industries as efficient bonding solutions. However, many customers focus only on adhesion strength or price when selecting tapes, overlooking the critical impact of tape structure (e.g., backing thickness, adhesive thickness) and performance on real-world applications. Choosing the wrong tape can lead to bonding failures, reduced productivity, or even product damage.
This guide explains the structure and performance of industrial tapes and provides recommendations for selecting the right tape based on substrate characteristics to ensure optimal application results.
Basic Structure of Industrial Tapes and Its Impact
An industrial tape typically consists of three core components: **Backing, Adhesive, and Release Liner. Each component’s structural parameters directly influence the tape’s performance.
- Backing (Carrier Material)
The backing provides mechanical support and determines the tape’s strength, flexibility, and temperature resistance. Common backing materials include:
– Polypropylene (PP) – Cost-effective, suitable for light-duty applications.
– Polyester (PET) – High strength and heat resistance, ideal for electronics.
– Polyvinyl Chloride (PVC) – Flexible, good for curved surfaces.
– Non-woven/Foam – Provides cushioning, suitable for uneven surfaces.
Impact of Backing Thickness:
– Thin Backing (<0.05mm) – Used in precision applications (e.g., smartphone display bonding).
– Medium Thickness (0.05-0.2mm) – General-purpose (packaging, signage).
– Thick Backing (>0.2mm) – Used for cushioning/sealing (e.g., automotive noise insulation).
- Adhesive (Bonding Layer)
The adhesive determines the tape’s bonding performance. Common types include:
– Acrylic – Weather-resistant, suitable for outdoor/high-temperature use.
– Rubber-based – High initial tack, good for quick fixes.
– Silicone – Heat-resistant (>200°C), used in electronics.
Impact of Adhesive Thickness:
– Thin Adhesive (<30µm) – Best for smooth surfaces (glass, metal).
– Medium Thickness (30-100µm) – Works on slightly rough surfaces (plastic, wood).
– Thick Adhesive (>100µm) – Ideal for rough/curved surfaces (foam, textiles).
- Release Liner (Protective Layer)
The release liner affects unwinding performance and storage stability. Common types:
– Glassine Paper – Economical, general-purpose.
– PET Release Film – High flatness, used in precision electronics.
– Silicone-Coated PE Film– Moisture-resistant, long-term storage.
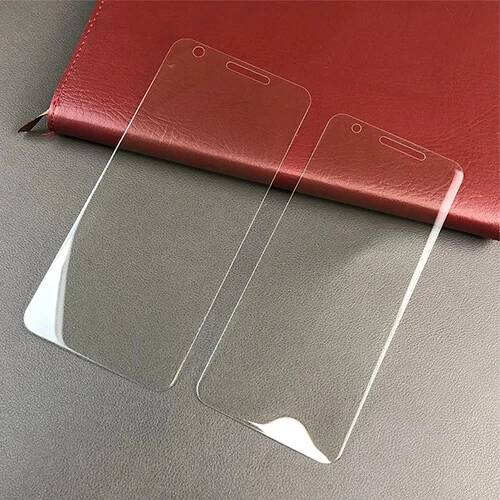
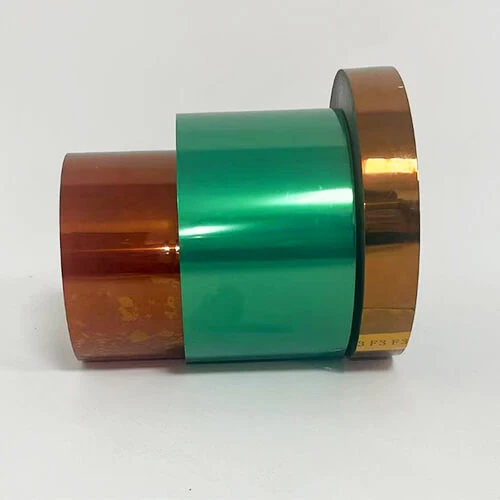
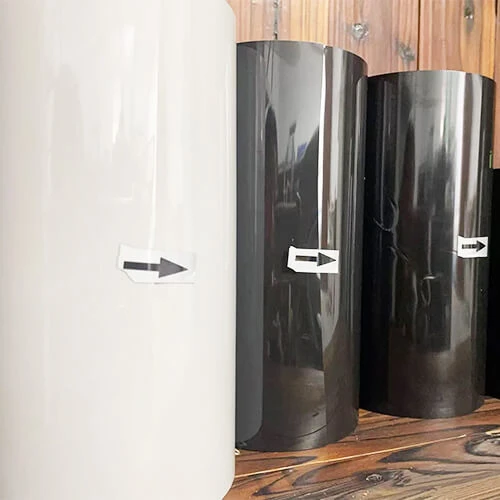
Tape Selection Based on Substrate Type
Different substrates require specific tape properties. Below are recommendations for common materials:
- Smooth Surfaces (Glass, Metal, Acrylic)
– Challenge: High surface energy but prone to stress-induced peeling.
– Recommended Tape:
– Backing: PET/PP film (0.05-0.1mm)
– Adhesive: Acrylic (30-50µm)
– Example: Clear double-sided tape, VHB foam tape.
- Rough/Porous Surfaces (Wood, Concrete, Textiles)
– Challenge: Uneven surface reduces adhesive contact.
– Recommended Tape:
– Backing: Non-woven/foam (0.2-0.5mm)
– Adhesive: High-tack rubber (>100µm)
– Example: Construction tape, carpet tape.
- Low-Surface-Energy Plastics (PP, PE, PTFE)
– Challenge: Poor adhesion with standard tapes.
– Recommended Tape:
– Backing: PET or modified PP
– Adhesive: Specialty acrylic (with tackifiers)
– Example: PP-specific tape, fluoropolymer-treated tape.
- Flexible/Curved Surfaces (Rubber, Foam, Silicone)
– Challenge: Material deformation causes tape failure.
– Recommended Tape:
– Backing: Elastic foam/silicone
– Adhesive: High-elongation adhesive
– Example: Stretchable tape, medical silicone tape.
- High-Temperature Environments (Electronics, Engine Bays)
– Challenge: Standard tapes degrade under heat.
– Recommended Tape:
– Backing: Polyimide (PI) or aluminum foil
– Adhesive: High-temp silicone (>200°C)
– Example: Kapton tape, heat-resistant foil tape.
How to Test Tape Suitability
Before full-scale use, conduct small-scale tests focusing on:
- Initial Tack – Immediate bonding strength.
- Shear Resistance – Long-term load-bearing ability.
- Peel Strength – Force required to remove the tape.
- Temperature Resistance – Performance under heat/cold.
- Chemical Resistance – Durability against oils/solvents.
Common Issues & Solutions
Problem | Possible Cause | Solution |
Tape peels off | Adhesive-substrate mismatch | Use higher-tack/specialty adhesive |
Residue left behind | Adhesive too soft/thin | Switch to high-cohesion acrylic |
Hard to unwind | Wrong release liner | Use low-release-force liner |
Fails under heat | Non-heat-resistant tape | Switch to silicone/PI tape |
Conclusion
Selecting the right industrial tape is not about “stronger is better” or “thicker is better.” Instead, it requires matching tape structure (backing, adhesive, thickness) to substrate properties (surface energy, roughness, flexibility, temperature resistance). The correct choice improves efficiency and reduces rework.
For further assistance in tape selection, contact our technical team for customized solutions!
Hope this guide helps you choose the right industrial tape for optimal performance! 🚀